Preoiling—The Ultimate Engine "TLC"
Oil is life's blood for an engine. Fuel may be the food that
keeps it running, but without oil, the engine will die in spite
of the fuel available. Normal procedures tell us to check for
oil pressure within 30 seconds of engine start. When the pressure
gage starts to rise, we feel assured that the engine is being
properly lubricated. But, has the engine been properly lubricated
just because we now have oil pressure? The answer is a resounding "No!"
It is now. But it wasn't!
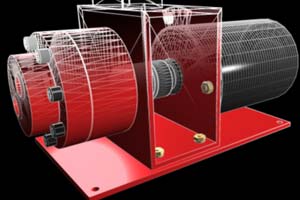 The Oilamatic Preoiler Unit
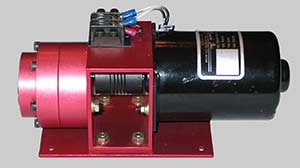
During
those brief moments from starter engagement, engine firing
and up to oil pressure rise, the engine runs without sufficient
lubrication. Depending on frequency and duration of operation,
very significant wear is attributed to this short interval
. If the engine is run frequently - every day - less wear
occurs during start because oil is retained on critical
surfaces. However, if the engine sits for long periods
- days, weeks or months - then the oil will evaporate and
drain from critical parts, and they will run without lubrication
until oil flows sufficiently to pressurize the entire system.
Some technical studies have shown as
much as 70% of total engine wear to this starting interval.
Eliminate that interval without oil and the engine should last
much longer.
Different parts of an engine have different lubricating needs.
Gears, such as those in the accessory section, need oil on the
surfaces to prevent distress. Gears without lubrication wear
badly. Lubricated gears last nearly indefinite. Plain bearings
- mains and rods - need oil at the onset of motion to prevent
contact between the crank journals and the bearings. Bearings
without lubrication wear rapidly. Lubricated bearings last nearly
forever.
Cylinder walls need oil to lubricate the pistons and piston
rings. Without lubrication, the pistons and rings wear quickly
and oil consumption increases rapidly. With lubrication - little
as is needed - pistons and rings have extended life with little
wear.
Cam lobes and lifters endure high loads even during start.
Without lubrication, both lobes and lifters gall badly (a la
Lyc O320 H2AD). With lubrication, both last for hundreds
of hours with little wear. Hydraulic valve lifters need oil under
pressure to operate properly. Without a constant flow of pressurized
oil, lifters collapse and take a pounding as the valve system
operates with excess clearance. With lubrication, the lifters
extend properly and valves operate with correct timing and little
undue distress. Valve stems and rockers require little oil to
operate. Yet, they still require some to avoid unnecessary wear.
Run while dry of oil, either one will experience undue wear.
Turbochargers require special attention during start to avoid
bearing and shaft wear. If the engine starts with little hesitation,
exhaust flows quickly and will initiate turbocharger rotation.
If there is no lubrication for the turbo's shaft, it will wear
quickly and will require a premature overhaul. If the shaft is
well lubricated before motion begins, very little wear will take
place, and the turbo's time to overhaul will be greatly extended.
In brief, all engine parts need lubrication at the first onset
of motion to keep wear to a minimum. Preoiling the engine by
pressurizing the lubricating system and pumping oil through it
before starting will eliminate that high wear interval usually
experienced during start.
Changing the oil and filter at regular intervals is preferred
preventive maintenance. Insidious as it may seem, however, this
maintenance item creates special conditions for wear. First,
oil must be sucked into the oil pump before flow begins. Second,
air in the filter must be purged before oil can flow to the engine.
In the process, purged air must be evacuated through the engine.
For a short time, air will lubricate critical engine parts while
it is pumped through the engine.
Air is purged easily from oil filters that mount upright (open
end up), and they remain filled with oil after engine shut down.
Horizontally mounted filters are also purged easily and remain
filled after engine shutdown unless air leaks into the filter.
Filters that install inverted, however, - Bonanza IO520's in
particular - empty after each shutdown and must be refilled during
each start. Anti-drain valves in the filter prevent oil back
flow into the crankcase, but air trapped in the inverted filter
turns it into an accumulator. Oil evacuation from the filter
is virtually guaranteed after engine shut down as the compressed
air forces the oil out of the filter and through the oil system.
Time to refill the filter is brief, but during that interval
oil flow is reduced and some air may again be forced through
the lubricating system with the oil. Wear takes place. Preoiling
will fill the filter with oil and purge the air. Wear from insufficient
lubrication will be eliminated.
Preoiling has requirements and limitations that must be observed.
First, pressure should be low enough to avoid harm to the engine.
In all aircraft engines, the oil pressure relief valve will serve
this function. Second, oil injected into the engine must be filtered.
Properly attached, a preoiler will inject engine oil into the
engine oil filter just as the engine driven oil pump does. Third,
no oil leakage should be created by preoiling. Normally aspirated
engines have no components of concern; however, turbochargers
require special limitations.
Installed
on a Piper PA30 Twin Comanchee
Most aircraft turbocharger shaft seals are not true seals that
would deny all oil passage. Instead, the seals are slip rings
that allow some oil to pass under pressure if there is no opposition.
During normal operation these seals rely on positive deck pressure
in the compressor housing/intake manifold and exhaust pressure
in the turbine housing to oppose oil pressure.
Most turbocharger installations also incorporate a scavenge
pump to draw the oil from the turbocharger housing. However,
when the engine is not running, none of these oppositions to
oil leakage exist. To the contrary, the scavenge pump acts as
a seal to prevent oil return to the crankcase. Continued preoiling
would build pressure in the turbo housing, and oil would be forced
out both compressor and turbine seals. Pressure cutoff switches
and/or strict limitations on preoiling time must be incorporated
to prevent undo leakage from the turbocharger. With these limitations,
turbochargers benefit tremendously from preoiling.
A preoiler can be used to lubricate an engine without starting.
Turn the preoiler on and spin the engine through several turns.
Oil will flow to all parts of the engine and the cold thick oil
will be slung onto all of the cold metal where it will stay for
an extended time. Engines with cylinder lubrication ports in
the connecting rods will also have well oiled cylinder walls.
Of course, if the preoiler is run for extended time without external
power, the battery will need recharging. If the engine is turbocharged,
the oil line to the turbo may have to be capped to prevent excess
oil leakage from the turbo seals. This is a small chore to insure
good lubrication to the rest of the engine.
Oilamatic, Inc. has been developing preoilers
for several different engine applications. Recently, they have
received FAA STC and PMA approval for preoiler installations
on several aircraft. Prices of kits range from $1395.00 to $1545.00
and include all fittings, wire and hardware. Hoses must be procured
separately.
The Oilamatic engine preoiler unit is a 12 or 24 volt electric
motor driven pump. The custom designed and manufactured pump
is plumbed into the engine oil system using special adapters
so that oil is drawn from the crankcase and injected directly
into the engine through the oil filter. The pump and motor are
sized to provide adequate preoiling for a cold engine while keeping
battery draw to acceptable limits. A check valve in the high
pressure side isolates the pump from the engine once the engine
is started and the pump is turned off. A dash mounted switch
operates the preoiler (with Master switch on). The pilot can
monitor preoiling on the engine oil pressure gage and turn the
pump off as the starter is engaged. Typical installations provide
oil pressure stabilized near the "bottom of the green" before
start. No air is left in the system, and all parts are lubricated
before their first motion. No matter how long the engine has
been sitting, it is fully lubricated before start instead of
after.
In summary, preoiling an engine can reduce that excess wear
attributed to insufficient lubrication during start or from ill
affects of long periods without operation. It is most comforting
to see the oil pressure gage reading in the "bottom of the
green" before the propeller starts turning. |